Texto
elaborado en base al redactado por el autor arriba mencionado.
DISEÑO Y CONSTRUCCION DE MECANISMOS DE CONTROL DE
MODELOS UCONTROL
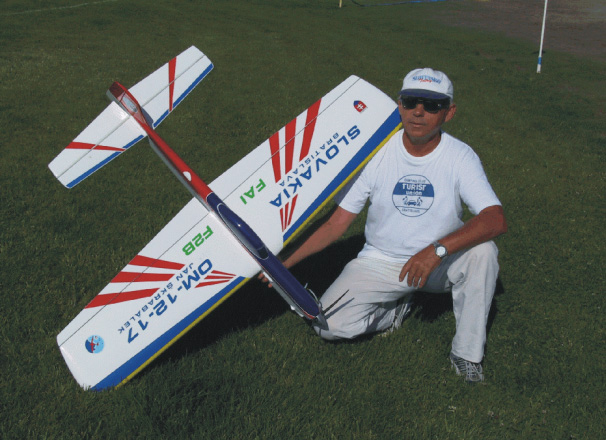
Jan Skrábalek
Los mecanismos de control deben estar correctamente diseñado
en términos de su ubicación en el fuselaje
del modelo y en términos de sus funciones cinemáticas
(confirmadas por análisis gráfico o matemático).
Podemos proceder al diseño y la construcción
(en forma de dibujos simplificados) y una construcción
práctica en el taller.
Se deben respetar los siguientes requisitos principales
al preparar una propuesta de diseño:
- minimización del número de componentes
principales,
- suficiente resistencia y rigidez de los
componentes con un peso mínimo,
- resistencias de fricción mínimas
de las conexiones móviles,
- vida útil suficientemente larga de las conexiones
móviles,
- buena producción tecnológica del mecanismo.
Al minimizar el número de componentes principales,
también aseguramos la minimización del número
de componentes mutuamente fijados.
La conexión de estos componentes en el mecanismo
de control, aumentan la seguridad del mismo contra fallos
y a la vez aumentará la vida del mismo.
Un ejemplo típico de minimizar el número de
componentes es la forma clásica del balancín
con el eje girando directamente en el mismo. Esta
es la forma clásica, hecha de una sola pieza de material
(duraluminio o chapa de acero, laminado, delrin, etc.) según
se ve en la figura siguiente.
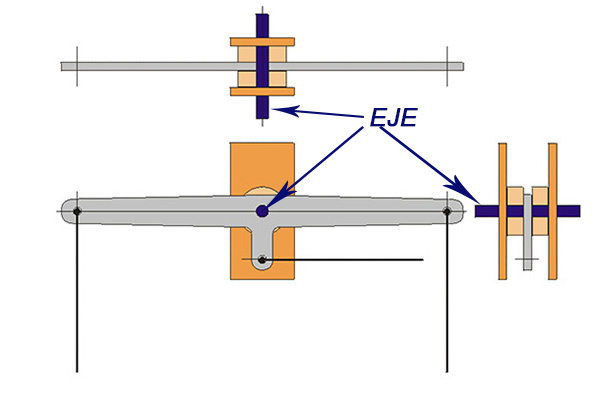
El balancin está montado de forma tal que gira
en el eje el cual está fijo en la parte
establecida para ello en el ala, tal como se muestra en
la figura anterior.
La posición axial del eje está asegurada por
fijación en el ala. Los cables y varillas de control
también se ubican y fijan simplemente en los agujeros
correspondientes.
La solución mencionada, aunque simple y fácil,
no cumple con el requisito de vida útil suficientemente
larga de las articulaciones giratorias. Por lo tanto, lo
usamos para modelos entrenadores o modelos de la categoría
F2D (combate), que en realidad son material de modelado
"consumibles".
Para prolongar la vida de las conexiones es mejor hacer
los balancines incorporando en los mismos un buje
metálico para giro en el eje, firmemente
conectado en el balancin y a la vez las salidas de lineas
forradas con nailon o teflón, según se muestra
en la figura siguiente.
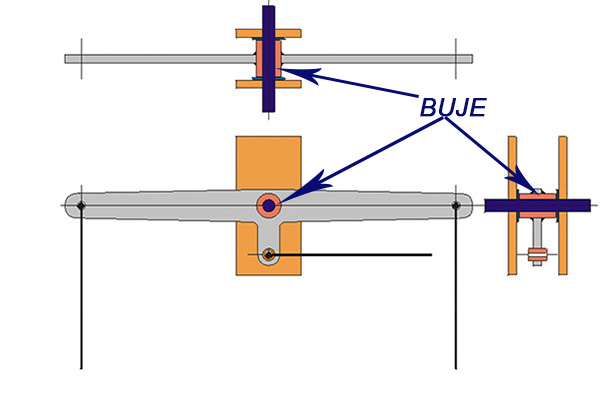
A
los agujeros para los cables de salida no es necesario embujar
porque el aumento de juego de los agujeros no es un problema.
Recientemente, el uso de modelos desmontables
se ha generalizado el uso del balancín expuesto por
fuera del ala a diferencia de los ejemplos anteriores, especialmente
para la categoría F2B. Esta novedad, además
de mejorar las condiciones de transporte, es una solución
que también trae la posibilidad de acceso directo
a las expuestas conexiones del mecanismo de control, así
como la posibilidad de ajustar las relaciones de transmisión
del mecanismo cambiando las longitudes de los brazos de
palanca individuales.
La
figura que sigue muestra la solución de diseño
utilizado en modelos desmontables. El "punto"
de giro del balancin está firmemente conectado a
un brazo pequeño fijado y solidario con
el giro del mismo. En el extremo de ese brazo o palanca
se fija la varilla (pushorod) de mando.
Al comparar esta solución con la solución
anterior, se puede ver que el número de componentes
ha aumentado y, lo que es más importante, se agregaron
dos importantes conexiones fijas de alta tensión,
que transmiten momentos de control entre las palancas.
En contraposición, en caso de falla de cualquiera
de estas conexiones, es inevitable un accidente modelo.
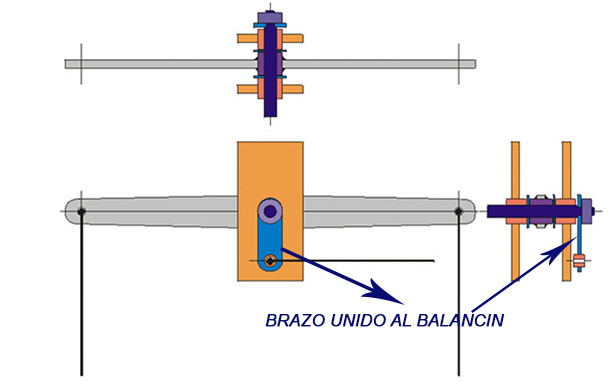
Otro
ejemplo típico de minimizar el número de componentes
principales es el diseño de las palancas o "cuernos"
de control de los flaps y elevadores, es en la forma que
se muestran en la figura siguiente.
CUERNOS DE FLAPS Y ELEVADORES
Los cuernos mencionados se pueden fabricar doblando una
pieza de alambre de acero (puede ser rayo de bicicleta o
motocicleta), para los flaps y elevadores como se muestra
en la siguiente imagen.
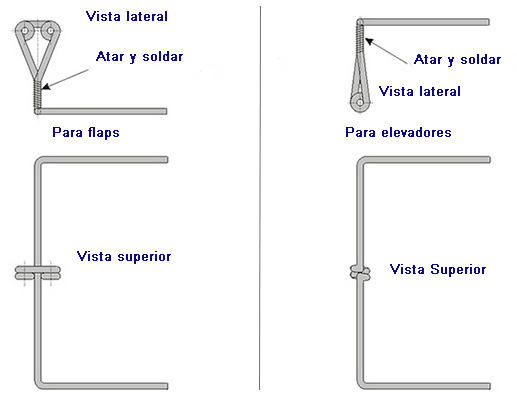
Esta solución de diseño la utilizó
durante muchos años J. Gabris en
sus modelos "SUPER MASTER" (Nota
1) sin las más mínimas
perturbaciones, ni un aumento notable del juego en las articulaciones
giratorias.
Desde el punto de vista de la fabricación, está
claro que para hacer tales cuernos se requiere una habilidad
adecuada que se obtiene practicando al doblar una gran cantidad
de alambres hasta lograr el buscado.
Para los modelos desmontables de la categoría F2B,
los cuernos de control de los flaps y elevadores se fabrican
en forma tal que permiten cambiar la longitud de los brazos.
Unas de las soluciones se muestran en la figura siguiente.
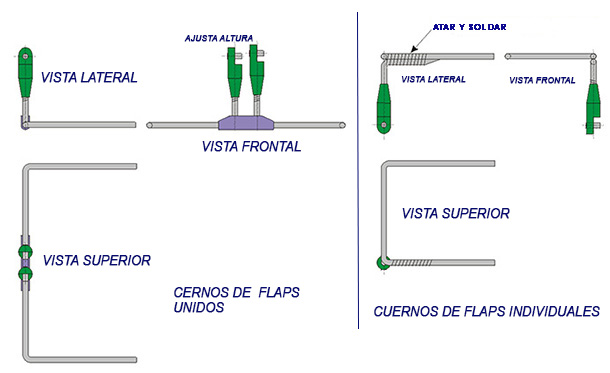
En la figura de la izquierda, los cuernos estan formados
por dos partes individuales, conectadas
por un "canal" fabricado en chapa de acero. Una
pieza hecha con duraluminio ajustable axialmente se atornilla
en la rosca del extremo de cada brazo donde se conecta el
pushrod.
En la figura de la derecha la conexión a los flaps
se ha hecho en dos partes separadas interconectadas
por alambre y soldadura. S.Cech utilizó
los cuernos con esta construcción en sus modelos
"UNO" (Nota 2).
Al comparar estas soluciones de diseño con la solución
de la figura anterior a esta, vemos que el número
de componentes principales y el número de sus conexiones
fuertes ha aumentado, lo que necesariamente se reflejará
en un aumento de peso y una menor confiabilidad. Esto sin
embargo, se compensa por la mayor capacidad de ajuste y
la facilidad de cambio de partes del mecanismo.
La figura que sigue muestra otro diseño comúnmente
utilizado en la fabricación de cuernos.
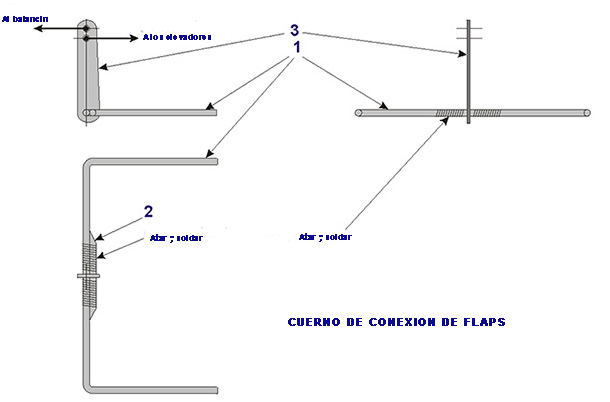
El cuerno o "palanca en U" del control de los
elevadores está hecha en ambos casos de una sola
pieza con un eje de alambre de acero en en el que se fija
un cuerno de accionamiento de chapa de acero con orificios
para su conexión con la barra de empuje (pushrod).
Garantizar la suficiente resistencia y fiabilidad de la
conexión del cuerno con el pushrod es resuelto doblando
el alambre en el área de la unión en su conexión
con un alambre soldándo en el lugar.
Todas las conexiones importantes del cuerno y los pushrods
en los flaps y los elevadores desde el punto de vista de
la confiabilidad se logran mejor utilizando soldadura con
plata. Soldar con estaño no garantiza seguridad
excepto para uniones donde no se requieren esfuerzos y en
estos casos es conveniente enrollar las partes con alambre
de cobre de 0.2 o 0.3 mm y luego soldar.
SALIDA
DE LINEAS
En
la figura siguiente, se mestran algunas formas de union
de las salidas de lineas.
En el ejemplo (A), se pasa el cable flexible
por cada agujero en el extremo del balancin,
se vuelve sobre el mismo pasando por un tubito metálico
el cual se presiona para ajustar ese cierre o se enrollan
las partes con alambre de cobre de 0.2 o 0.3 mm soldando
con estaño. Esto se hace también en el otro
extremo de la salida de la linea en el ala. Las lineas de
vuelo se unen con un mosquetón a estas salidas de
línea.
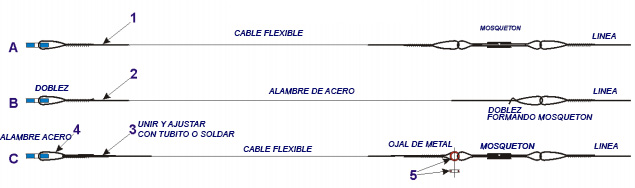
En la versión (B) para las salidas de lineas se utiliza
alambre de acero en lugar de cable flexible.
En la conexión con el balancin, se realiza el doblez
y cierre en forma similar a lo enunciado para el caso (A)
y en el extremo de salida en el ala, se forma un gancho
que a la vez sirve como mosquetón.
La desventaja de esta realización es la alta rigidez
a la flexión, provocando incluso que el alambre sufra
curvaduras durante el transporte. La flexión accidental
de cables es una causa común de atascamiento de cables
en la salida final enel ala.
La versión (C) está hecha combinando alambre
de acero y cable flexible y elimina las desventajas de la
versión (A) y (B).
El punto de conexión con el balancin está
hecho de alambre de acero y el mismo se conecta al cable
mediante envoltura con el extremo del cable en la posición
1, y una segunda vuelta con el extremo del cable en la posición
2 y soldando.
Para la conexión de los cables de salida con las
lineas de vuelo, en su extremo se coloca un anillo
de metal (5) asegurando de esta forma una larga
vida a esa unión.
Para la unión de los cables es preferible básicamente
usar un conector de hojalata. El uso de soldadura fuerte
provocaría cambios estructurales material del cable
causado por alta temperatura y un cambio de en la rigidez
de flexión entre el tramo soldado y la parte no soldada
del cable, con un impacto negativo en la resistencia por
fatiga del cable. Tambien es necesario limpiar a
fondo las juntas soldadas de los residuos
de ácido.
PUSHRODS
El último elemento estructural principal de los mecanismos
de control son las varillas de mando o "pushrods".
En la figura siguiente se muestran varios diseños
de uso común.
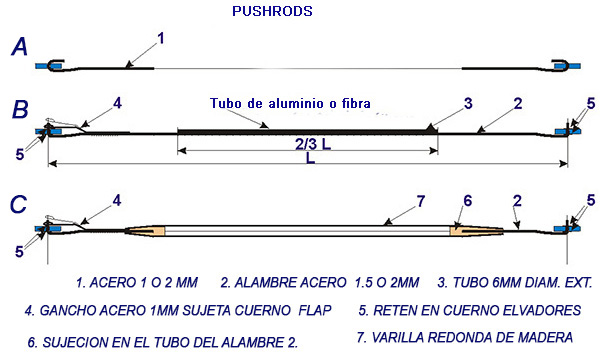
En (A) el pushrod está hecho de una sola pieza de
alambre de acero y después de pasar
a través de los orificios de los cuernos correspondientes
se asegura contra caídas doblando los extremos en
forma de "U". Esta versión es
muy simple, pero con posible corta vida útil de las
juntas giratorias y holgura relativamente grande solo es
adecuada para modelos de entrenamiento, modelos categoría
F2D, o para controlar funciones auxiliares para las categorías
F4B (escala).
En (B) el pushrod también está hecho de una
conexión a los cuernos con alambre de acero en ambos
extremos unidos mediante un tubo de fibra de carbono o aluminio
de un largo de 2/3 del total. Dar forma de "L"
a los extremos proporciona un área de contacto más
grande en el cuerno y menos juego en las conexiones con
los mismos, que aún pueden ser
complementado con arandelas para aumentar la vida útil
de la conexión.
El pushrod está asegurado contra salidas del cuerno,
soldando un alambre fino de acero a modo de retén
o resorte (5) permitiendo un fácil montaje y desmontaje
del pushrod.
En el caso de utilizar varillas de alambre en lugar de los
tubos antes mencionados, la rigidez puede aumentarse en
su elastisidad doblándolos en la parte media, o utilizando
dos alambres, que en la parte media doblamos
en forma cruzada. Este cruce es ventajoso al ajustar las
posiciones básicas de los cuernos al montar el mecanismo
de control.
Si descubrimos del análisis gráfico de la
función cinemática que la varilla realiza
un movimiento de balanceo alrededor de la parte media (se
mueve axialmente), podemos colocar una guía en el
lugar de la flexion.
En
(C), se muestra otra forma que que está en contra
de la solución (B) preferiblemente en términos
de peso mediante uso de un tubo liviano de fibra o de madera
redonda dura. El ajuste de la longitud exacta de la varilla
es posible gracias a una rosca conectando cada un extremo
de la misma.
Es una conexión útil en pushrods de flaps
y elevadores.
Nota
1: Gabris (chekoslovakia) ganó el FIA F2B WC dos
veces con este modelo: 1966 en Inglaterra y 1968 en Finlandia
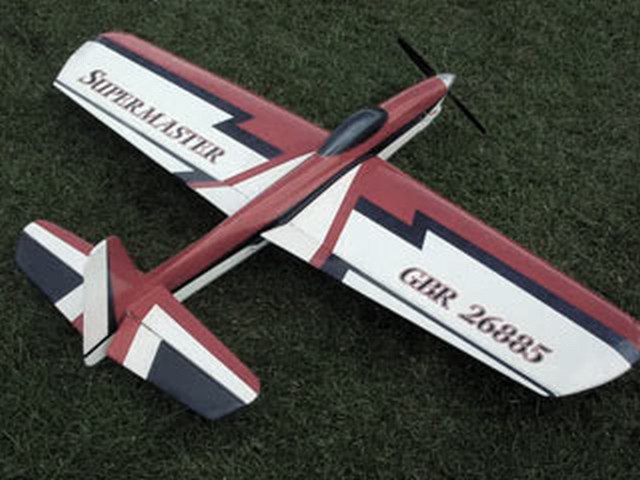
Hacer click
aqui para bajar el plano
Nota
2: "UNO" modelo de Stanislav Czech ganador del
Campeonato de Europa de F2B en 1983,
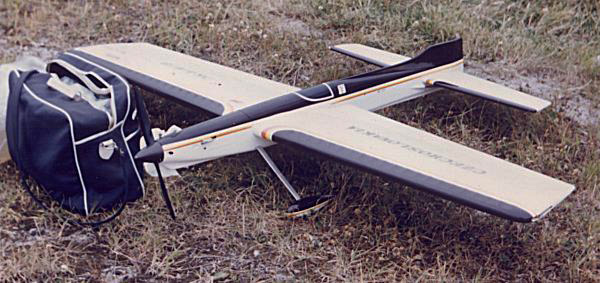
Hacer
click aqui para bajar el plano