Amigos, en esta oportunidad quiero acercarles
unos cuantos Tips de construcción (Trucos de taller si los
quiere llamar así), una gran mayoría los comenta Al Rabe en
la construcción de su Mustunt IV, otros los fui rescatando
por ahí…
Como dije recién, Al Rabe enseñó su forma de
hacer algunas cosas, algunos procesos, que si bien los
muestra en el desarrollo del Mustunt IV, los aplica
constantemente en la construcción de todos sus modelos.
Tren de aterrizaje y soporte de balancín
En la siguiente secuencia de fotografías se
aprecia la infraestructura para soportar el tren de
aterrizaje que el autor confeccionó con el habitual alambre
acero de 1/8”
El soporte del alambre de acero que va
solidario a la costilla lo realiza con un sándwich de
terciadas, primero una de 1/32” (0,8 mm) -que pega sobre la
costilla- luego van las tres partes que se ven en la
fotografía de terciada de 1/8” por donde pasa el alambre de
acero y finalmente cierra el conjunto con otra terciada de
1/32”.
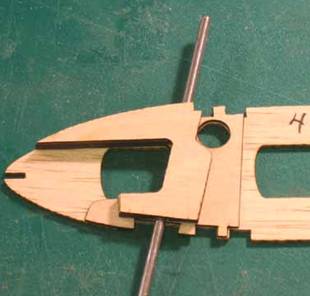
Como
este tren funciona como barra de torsión, va a necesitar una
plataforma que sostenga el alambre en forma horizontal
(entre dos costillas). Como verá en la siguientes dos
fotografías, también utiliza terciada de 1/8”, una con un
ranura para contener/sostener el alambre y otra –pegada a la
anterior- para dar fortaleza al conjunto. Nota: En la foto
de la izquierda se está “presentando” en conjunto sobre las
costillas, aquí están las dos terciadas, pero en la foto de
la derecha cuando ya está todo pegado no está la segunda
maderita …se ve que la pegó después, vaya uno a saber, lo
que si creo que tiene que estar si o si.
En la fotografía se aprecia que utilizó
tuercas de empotrar. Las mismas fueron fijadas con
cianocrilato a la madera y después les repasó la rosca con
un macho por las dudas
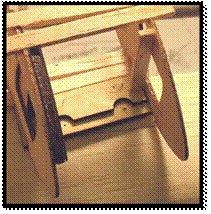 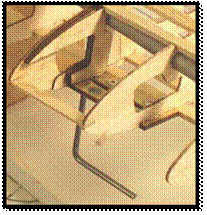 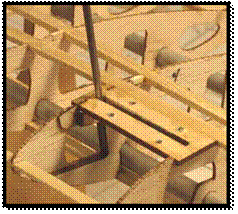
Al Rabe habitualmente realiza un enchapado
integral del ala, motivo por el cual debe cuidar al máximo
el peso de todos los componentes del modelo, personalmente
pienso que la estructura que realizó para sostener el tren
es más liviana y resistente que colocar los palitos de
madera dura de 10x10 y también creo que no agrega demasiado
trabajo adicional hacer esta confección.
Exactamente el mismo método de realizar un
sándwich de terciadas también lo utiliza para sostener el
balancín:
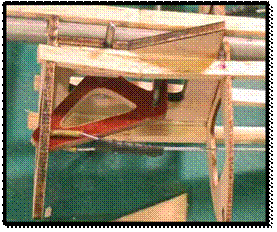
Observe con detenimiento la fotografía
anterior. Vea que utilizó un material tipo Micarta para
confeccionar el balancín, que lo colocó en forma invertida
para que el cable “arriba” del timón de profundidad quede
delante de “abajo”, que no utiliza bujes pero si coloca el
leadout (cables de salida) dentro de un tubo muy fino de
bronce –que también he visto de cobre- y, fundamentalmente,
el soporte tiene una saliente –hacia arriba, por fuera del
ala- que utilizará para trabar el ala con el fuselaje …será
que el Sr. Rabe teme que le arranquen el ala del fuse cuando
realizan la prueba de tensión de líneas???
Borde de fuga y bisagras
En las próximas fotografías se puede apreciar
que utiliza Balsa de 3mm para la confección del borde de
fuga, que es más liviano y mucho más fácil del perfilar que
un listón de 5 o 7 mm, ni hablar si utiliza uno de 10 mm
Vea que con dos piezas rectangulares, también
de balsa de 3mm, hace los bolsillos para contener las
bisagras, también podrá apreciar que la deriva, el timón de
dirección y los elevadores están realizados a partir de
planchas de balsa (huecos). Le vuelvo a repetir, Al Rabe
suele trabajar con estructuras totalmente cerradas que,
luego de forradas con recubrimiento y pintadas hacen una
estructura sumamente dura y rígida, si, suman peso, pero la
terminación que le puede dar a sus modelos es excelente.
Respecto al recubrimiento, debo comentar que
Al Rabe hizo el 100% del recubrimiento con fibra de vidrio y
epoxy, él dice que podría haberlo realizado con Dope –en
lugar del epoxy- y que no recomienda hacerlo de esta forma
ya que da mucho trabajo, aunque reconoce que el modelo queda
totalmente fuel-proof.
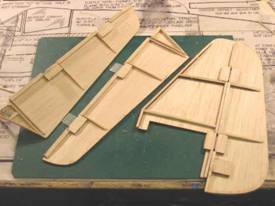
Cuerno y Push-rod
Me parece muy interesante lo que Al Rabe hace
con el cuerno del Flaps, es de realización casera y lo
coloca antes de enchapar el ala, bien ajustado con hilo y
cementado. La soldadura entre el alambre y el brazo lo
realiza en bronce, y con estaño los tubos que unen los push-rods,
que dicho sea de paso, estos tubitos son de bronce de 3/32”
de diámetro interior. El push-rod que va desde el balancín
hasta este cuerno no tiene regulación (es de acero de 3/32”
doblado a la longitud necesaria) y tiene soldada con estaño
una arandela para evitar que se salga de su posición.
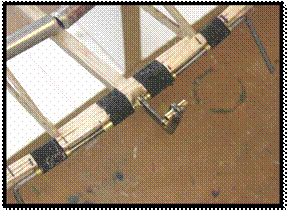 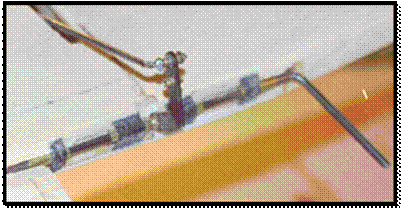
Acá les dejo otra forma de terminar el push-rod
muy interesante que tal vez ustedes ya conozcan:
Aquí el push-rod es de carbono y tiene una cupla
de aluminio donde se enrosca un tramo de un
tornillo de bronce donde está soldado el alambre
que se ve en la fotografía, obviamente, la
longitud de este push-rod es ajustable. |
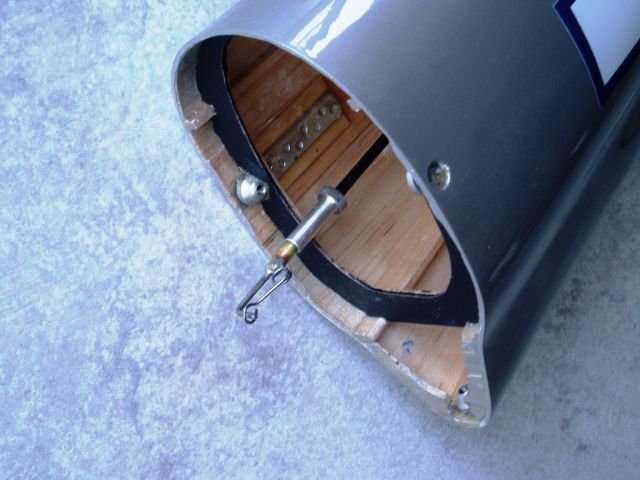 |
Patín de cola
Les muestro algo muy sencillo de implementar,
aunque en la práctica muy pocos hacen: soldar al patín de
cola un alambre para utilizar un largador manual del modelo.
Al Rabe extremó la seguridad y agregó un
tramo de leadout (cable de salida) soldado a los dos
alambres de acero y sujeto mediante hilo a la terciada que
sostiene el conjunto.
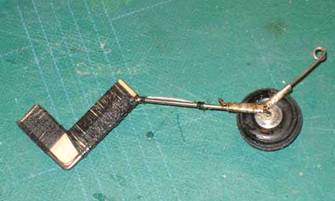
Es muy interesante saber que el conjunto
terminado (como se puede apreciar en la foto
superior-derecha) queda muy robusto y, a la hora de pegarlo
al fuselaje, las ataduras de hilo no presentan ninguna
dificultad con los pegamentos.
Conector en el Leadout
Esto que sigue me pareció espectacular para
mostrarles, no por lo novedoso, sino porque es la solución
implementada en el tan codiciado Classic 3 de Juriy Yatsenko.
Al
ver esta foto (la de más arriba) lo primero que pensé fue
que se trataba de una solución demasiado casera para la
talla del Classic 3, pero si está ahí es porque funciona y
es liviano –en comparación con alguna otra solución- Mi
imaginación me dice que Yuriy realizó un conector con
alambre de acero de 1mm soldado al cable de salida
–previamente atado con un hilo de cobre tomado de un tramo
de conductor eléctrico- y la traba fue realizada con tubo de
bronce aplastado y el extremo libre del conector tiene un
pequeño doblez hacia afuera para que la traba no se deslice
con facilidad (hay que apretar con cierta presión para sacar
la traba y poder sacar/poner el ojal de las líneas de mando)
…y justo necesité hacer los conectores de los cables de
salida de un modelito, así que hice una prueba para ver cómo
quedan. Funciona bien y me ahorro un par de conectores
(mosquetones) deslizables del tipo “Sullivan” que ahora
están complicados de conseguir.
Les adjunto dos fotos de los conectores que
hice:
Borde de
ataque
Tener un borde de
ataque sin un súper listón de balsa tampoco es
novedad. Un enchapado integral es muy liviano y
tiene excelente resistencia a la torsión, en
este caso, es ayudado por una varilla de balsa
puesta en forma transversal. Recuerde que el
modelo está hecho para volar, no para romperse,
de todos modos no hay ninguna receta mágica para
la piña de frente, a fondo, contra el piso.
Lo mas importante de lo que les mostraré es que,
ante la necesidad de unir maderas para formar el
enchapado, es dejar la parte del borde de ataque
propiamente dicho sin uniones, es decir, coloque
la plancha entera en el centro y realice las
uniones en los bordes -en forma simétrica-, para
lograr el ancho total que necesita. |
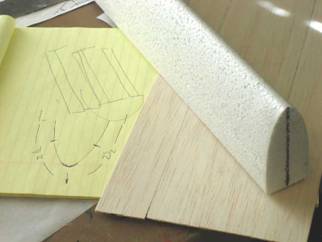 |
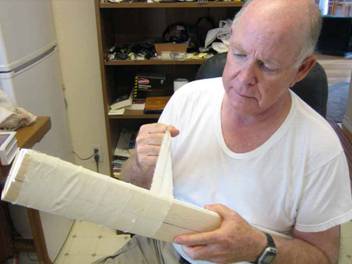
La unión de
las planchas se realiza con cianoacrilato
(ya que luego deberá sumergir la madera en
agua), este pegamento
es preferible porque aquí no haya uniones
rígidas para que la madera no se quiebre.
Obviamente para este procedimiento será
menester la correcta selección de la madera. |
Al recomienda una tabla grado
“A” de 6-7 lb -de 2mm de espesor- para la
parte central, para los extremos no es tan
crítica esta selección ya que el radio de
curvatura que deberá tener no es tan
notorio, pero advierte que la madera dura es
mucho más pesada, tampoco recomienda la
balsa sumamente blanda.Una vez que tiene las
planchas unidas la sumerge en agua dentro de
la bañera, no especifica si utiliza agua
fría o caliente; aclara que con media hora
es suficiente, pero él las deja una hora o
algo más. Al sacarlas, las coloca sobre el
molde con la forma que deberán tomar –hecho
con poliestireno expandido- y las ajusta con
tiras de tela hechas de sábanas viejas,
prestando especial atención en que la balsa
no se vaya desplazando del molde. Por
seguridad, Rabe coloca dos listones de
aluminio –como se muestra en la fotografía-
y agrega una segunda capa de recubrimiento
con tela para que todo el conjunto quede
bien derechito. Deja secar al sol un día …y
listo! …si si, después saca las vendas. |
Esto es todo, amigos. |